Allt när det gäller stål och metaller
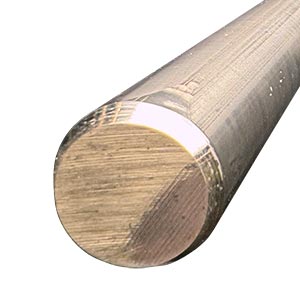
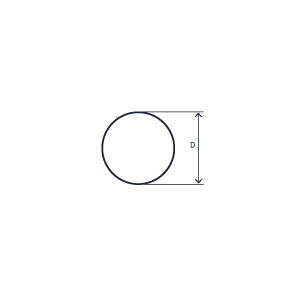
- Enhet
- Antal
-
- Radmärke
Vill du bli kund?
Ansök om kundkontoProduktinformation
De austenitiska stålen med beteckning 1.4301 (SS 2333) och 1.4307 (SS 2352) utgör den absolut vanligaste typen av rostfritt och innehåller ca 18% krom och 9% nickel. Skillnaden mellan de två sorterna är att 1.4301 tillåts ha lite högre kolhalt än 1.4307 vilket har som konsekvens att 1.4301 uppvisar marginellt högre hållfasthet. I praktiken är dock skillnaden i kolhalt mellan 1.4301 och 1.4307 ofta av ringa betydelse. Om stålet ska svetsas bör 1.4307 ändå väljas eftersom 1.4301 kan annars uppvisa nedsatt korrosionsbeständighet i området intill svetsen.
I form av dragen rundstång är 1.4301/1.4307 standardiserat i SS-EN 10088-3. Standarden omfattar kallbearbetad rundstång med diameter t o m 250 mm men normalt är det enbart de mindre dimensionerna som finns tillgängliga i kalldraget utförande. Vårt program omfattar stång med diameter t o m 30 mm.
Stålen 1.4301 och 1.4307 karakteriseras av god korrosionsmotstånd vid kontakt med vanligt, neutralt vatten såväl inomhus som utomhus. Beständigheten mot atmosfärisk korrosion är också god. Dessa stålsorter utgör dock ett mindre bra val om miljön är sur eller om den innehåller klorider. Då krävs stål med högre legeringsinnehåll.
Dragen stång av 1.4301 och 1.4307 bibehåller ganska bra kallformbarhet trots att duktiliteten har sänkts genom kallbearbetning. Stålen karaktäriseras dessutom av utomordentligt svetsbarhet. Austenitiska stål såsom 1.4301/1.4307 är allmänt besvärliga att maskinbearbeta men bearbetningen underlättas av för ändamålet anpassade verktyg. Om bearbetbarheten är av betydelse för applikation i fråga bör det svavellegerade austenitiska stålet 1.4305 övervägas.
Ytbeskaffenhet på 1.4301/4307 i lager är 2H såsom den definieras i SS-EN 10088-3. Kalldragning sker efter att den varmvalsade stången har glödgats och betats men ändock kan vissa små ytfel kvarstå. Av denna anledning bör den kalldragna ytan inte lämnas obearbetad om detaljen eller konstruktionen kommer att utsättas för hög belastning. Diametertoleransen är h9 enligt ISO 286 - 2 som är en noll-minus-tolerans. Med andra ord är diametern marginellt mindre än den nominella. Rakheten är god med pilhöjd mindre än 0,001 x längd.